In the materials engineering labs at UBC, surrounded by Bunsen burners, microscopes and spinning machines, professor Frank Ko and research scientist Addie Bahi have developed a simple process for converting waste cotton into much higher-value nanofibres.
These fibres are the building blocks of advanced products like surgical implants, antibacterial wound dressings and fuel cell batteries.
“More than 28 tonnes of cotton are produced worldwide each year, but very little of that is actually recycled after its useful life,” explains Bahi, a materials engineer who previously worked on recycling waste in the United Kingdom. “We wanted to find a viable way to break down waste cotton and convert it into a value-added product. This is one of the first successful attempts to make nanofibres from fabric scraps – previous research has focused on using a ready cellulose base to make nanofibres.”
Compared to conventional fibres, nanofibres are extremely thin (a nanofibre can be 500 times smaller than the width of the human hair) and so have a high surface-to-volume ratio. This makes them ideal for use in applications ranging from sensors and filtration (think gas sensors and water filters) to protective clothing, tissue engineering and energy storage.
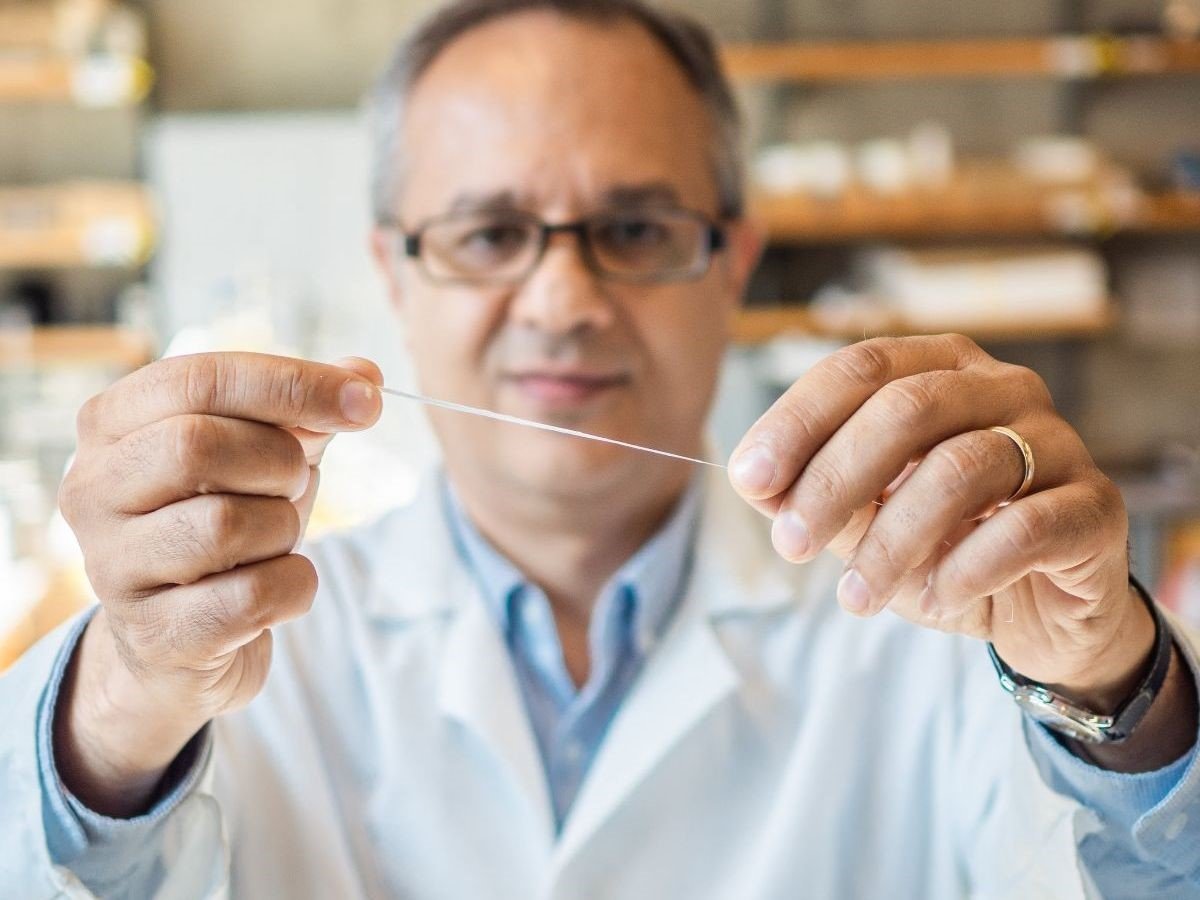
Ko and Bahi developed their process in collaboration with ecologyst, a B.C.-based company that manufactures sustainable outdoor apparel, and with the participation of materials engineering student Kosuke Ayama.
[ad_336]
They chopped down waste cotton fabric supplied by ecologyst into tiny strips and soaked it in a chemical bath to remove all additives and artificial dyes from the fabric. The resulting gossamer-thin material was then fed to an electrospinning machine to produce very fine, smooth nanofibres. These can be further processed into various finished products.
“The process itself is relatively simple, but what we’re thrilled about is that we’ve proved you can extract a high-value product from something that would normally go to landfill, where it will eventually be incinerated. It’s estimated that only a fraction of cotton clothing is recycled. The more product we can re-process, the better it will be for the environment,” said lead researcher Frank Ko, a Canada Research Chair in advanced fibrous materials in UBC’s faculty of applied science.
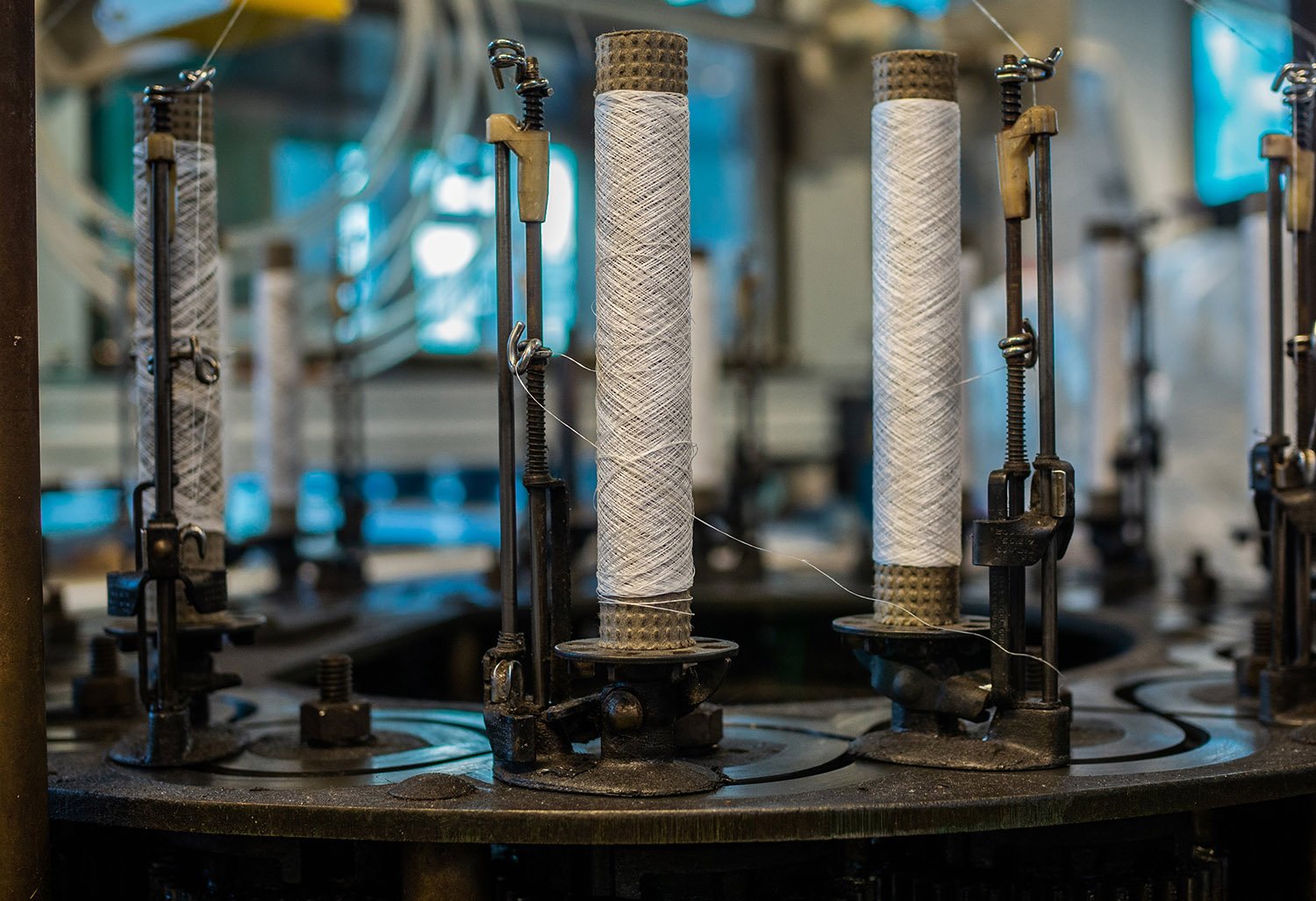
[rand_post]
The process Bahi and Ko developed is lab-scale, supported by a grant from the Natural Sciences and Engineering Research Council of Canada. In the future, the pair hope to refine and scale up their process and eventually share their methods with industry partners.
“We started with cotton because it’s one of the most popular fabrics for clothing,” said Bahi. “Once we’re able to develop the process further, we can look at converting other textiles into value-added materials. Achieving zero waste for the fashion and textile industries is extremely challenging – this is simply one of the many first steps towards that goal.”